「衝突試験の変形量と解析値が大きく乖離している。」
「落下解析の応力集中部と実験の破損部が一致しない。」
そんなお話をよく伺います。これらの解析の精度を上げたいという要望がある場合、皆様が検討されている項目は大きく分けて二つある印象です。一つは材料モデルの再検討。こちらは高速引張などの実験で物性値を取得しなおします。もう一つは、解析と実験値の乖離を確認してモデルを修正していく方法です。
特に、後者に関して非接触で3次元変位・ひずみ分布が計測できる”デジタル画像相関法”は有効です。このデジタル画像相関法では、対象にランダムなパターン模様を塗布し、その模様を追跡することで変位・ひずみ分布を計測します。例えば、30 cm×30 cmの範囲に数万点の多軸歪ゲージを貼り付けてデータをとるような網羅的なデータ取得が可能な技術です。応用先も広く、弊社Webサイトで事例の紹介もしております(https://dic.kke.co.jp/)。
最近、弊社ではこの計測技術に加えて、OEM出身の弊社構造解析技術担当者の知見も組み合わせて、ご相談に対応する体制が整いました。
例えば、自動車OEMメーカー様、サプライヤー様では、解析対象が複雑なコンポーネントとなるので、解析と実験値はそもそも乖離しやすいです。特に溶接部や部品組付け部が衝撃を受けた時の振る舞いを予測することが難しいため、境界条件の設定が課題となります。加えて、マルチマテリアル化など元々モデルの構築が難しい対象や、樹脂のように高速度の解析が難しい素材も増えています。やはり、これらの開発・設計の工程をスムーズとするためにも、CAE強化は必要なインフラ整備といえます。デジタル画像相関法は落錘試験、衝突試験やスレッド試験などでCAE検証を行う際に非常に有効な手段だと考えております。境界条件の検証やCAEと実験値の乖離を具体的に評価できます。また、弊社ではOEM構造解析担当者の視点から、解析検証に有効な測定方法をご提案するように心がけています。
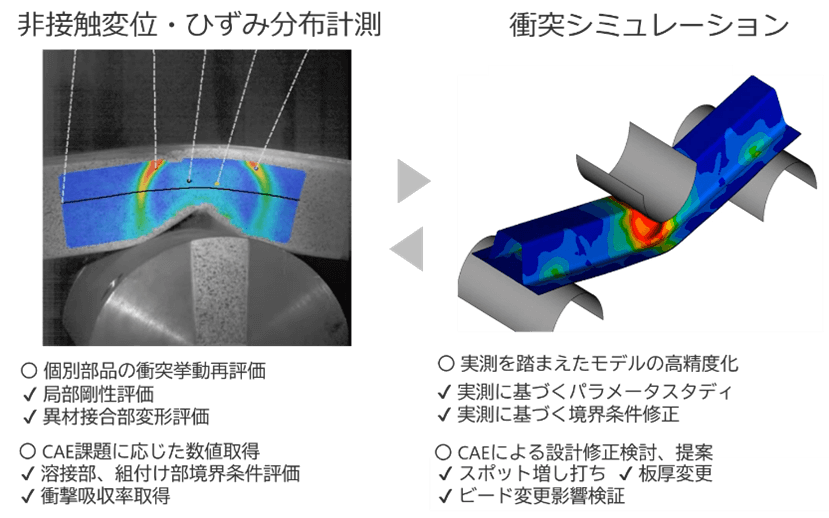
近年のこの手の計測技術の発展は目覚ましいものがあります。例えば、エアバック展開の姿勢・形状評価なども可能になりました。蛇足ですが、下図に示すようなスレッド試験の計測だけではなく同一ソフトウェア上で模擬的にCADを動かすこともできます。早い段階で、ダミー人形の頭部が周囲の部品とどのように干渉するのかを検証できます。
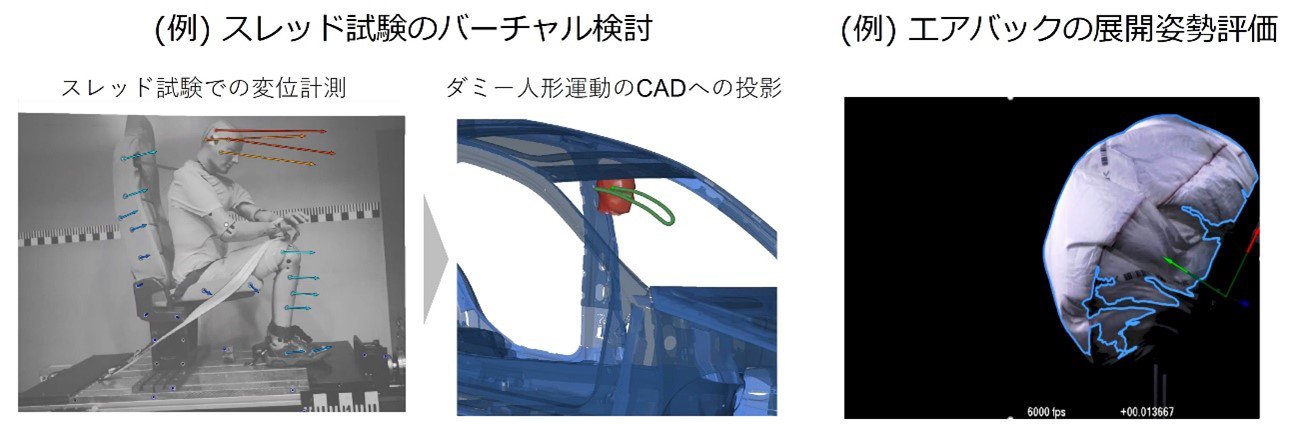
他にも、機械メーカー様では利用中・運送中の落下を想定した設計検証なども良く実施されていると伺っております。落下の応力集中を緩和するためのリブは、想定通り機能しているかなど検証するのは非常に困難です。弊社では落下の計測による性能検証だけではなく製造工程変更による歪み、われ、欠けなどの原因追及もお手伝いしております。わかりやすい落下計測事例はWebサイトでもご案内しております。
(https://dic.kke.co.jp/case/drop-smartphone/)
ご興味ございましたら詳細もご説明可能です。下記までお気軽にお声がけください。