今回の技術コラムは新人によるHiramekiWorksの体験記となっています。
構造最適化ソフトウェアであるHiramekiWorksを用いて、新人がロボットアームモデルの軽量化に取り組んだ内容です。
COLUMN
技術コラム
【構造最適化】番外編:新人によるHiramekiWorksの事例作成体験記
ロボットアームの軽量化
Fig.1(A)に軽量化を施すロボットアームのモデルを示します。モデルのロボットアームは、SOLIDWORKSで作成しています。今回の軽量化の対象はArm_1とArm_2の2本のアームです。
Fig.1(B)は様々なロボットアームを参考に、よくありそうな軽量化モデルを自分で作成したものです。
![]() |
![]() |
(A)原型モデル 体積:2.22x10 mm |
(B)自分で軽量化したモデル 体積:2.05x10 mm |
体積を減らして軽量化してみたものの、剛性は大丈夫なのかということで、この2つのモデルに荷重をかけた際の最大変位量を比較してみます。荷重条件と結果をFig.2に示します。
![]() |
![]() |
(A)原型モデル 最大変位:3.86x10 mm |
(B)自分で軽量化したモデル 最大変位:8.91x10 mm |
Fig.2のように、アームの部分の軽量化はできている一方で、最大変位が大きく増加してしまいました。いくら軽量化できても、剛性が低くなってしまうのはよくないですよね。ということで、自分で軽量化したモデルと同じくらいの体積で、より剛性が高い形状を見つけ出すためにHiramekiWorksを使って、構造最適化を行っていきます。一度に全体の構造最適化の行うことはできないので、Arm_1とArm_2を順に行っていきます。全体の流れをFig.3に示します。
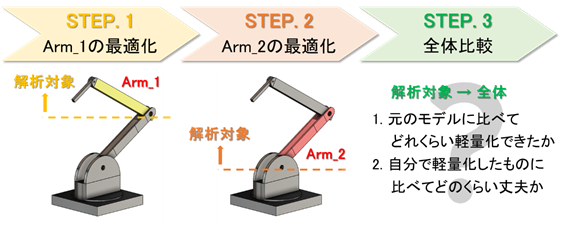
STEP.1:Arm_1の構造最適化
Arm_1の構造最適化をするにあたってHiramekiWorksを用いて、モデルに穴を開けたり削ったりするトポロジー最適化と、モデルの形状を変更する形状最適化を行いました。トポロジー最適化で体積を減らし、形状最適化で剛性を増加させることで、ある程度剛性を保ったまま軽量化することを目指します。Fig.4に荷重条件、Fig.5に最適化の条件と結果を示します。
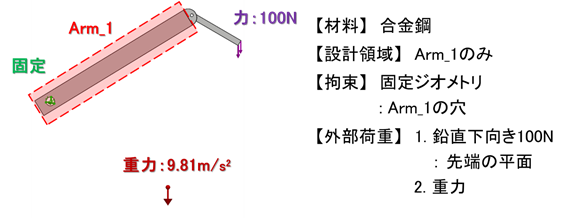
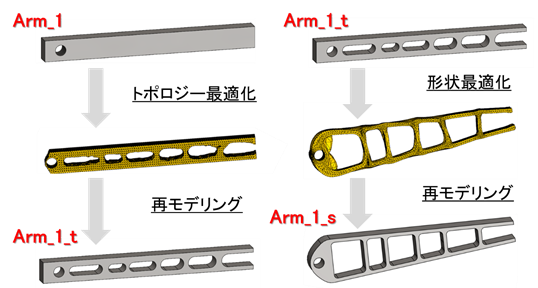

Fig.4の荷重条件でArm_1にトポロジー最適化をすることで、いくつも穴が開いた形状が得られました。これをきれいに再モデリングしたものがArm_1_tです。
続いて、Arm_1_tに形状最適化をすることで、穴が大きくなり幅が広がっていく形状が得られました。これを、きれいに再モデリングしたものがArm_1_sです。最適化で得られる形状はいびつなので、再モデリングをする必要があります。何度もモデリングと解析を繰り返して最終的な形状を決めていきます。
Arm_1の軽量化がうまくいっているかどうかをFig.4の荷重条件で、原型であるArm_1と最適化後のArm_1_sにおける体積と最大変位量を比較することで検討します。解析結果がFig.6です。
![]() |
![]() |
体積:1.76x10 mm 最大変位:2.12x10 mm |
体積:1.00x10 mm 最大変位:1.94x10 mm |
Fig.6より、トポロジー最適化と形状最適化によって、原型モデルより体積が約40%減少し、最大変位も小さくなっています。すなわち、Arm_1においてある程度剛性を保ちつつ軽量化できたと言えます。
STEP.2:Arm_2の構造最適化
STEP.2ではArm_2の最適化を行っていきます。STEP.1同じようにトポロジー最適化と形状最適化を行い、ある程度剛性を保ったまま軽量化することを目指します。Fig.7に荷重条件、Fig.8に最適化の条件と結果を示します。
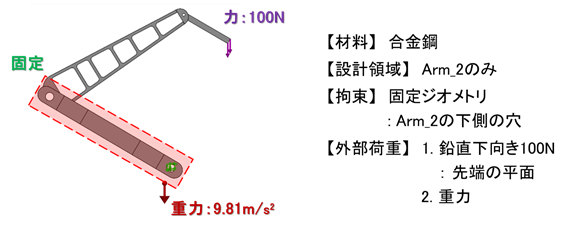


Fig.7の荷重条件でArm_2にトポロジー最適化をすることで、中がくりぬかれて柱が2本立ったような形状が得られました。これをきれいに再モデリングしたものがArm_2_tです。続いて。Arm_2_tに形状最適化をすることで、柱の幅が幅と左側のくりぬかれた断面が広がっていく形状が得られました。これを、きれいに再モデリングしたものがArm_2_sです。モデリングと解析を繰り返す中で、柱の広がりは最大変位にあまり影響していないことが分かったので、Arm_2_tからArm_2_sにかけては左側の断面を主に修正しています。
STEP.1と同様にFig.7の荷重条件で、原型であるArm_2と最適化後のArm_2_sにおける体積と最大変位量を比較することである程度剛性を保ったまま軽量化できたかを検討します。解析結果がFig.9です。
![]() |
![]() |
体積:1.96x10 mm 最大変位:2.12x10 mm |
体積:9.00x10 mm 最大変位:2.95x10 mm |
Fig.9より、トポロジー最適化と形状最適化によって、原型モデルより体積が約50%減少し、最大変位もさほど増加していません。すなわち、Arm_2において程度剛性を保ちつつ軽量化できたと言えます。
STEP.3:全体比較
2本のアームの軽量化ができたので、最後に全体で比較します。自分で軽量化したモデルとHiramekiWorksで軽量化したモデルをFig.10に、2つの軽量化モデルに初めと同じ荷重条件を加えた結果をFig.11に示します。
![]() |
![]() |
![]() |
原型モデル 体積:2.22x10 mm |
自分で軽量化したモデル 体積:2.05x10 mm |
HiramekiWorksで軽量化したモデル 体積:2.04x10 mm |
![]() |
![]() |
![]() |
原型モデル 最大変位:3.86x10 mm |
自分で軽量化したモデル 最大変位:8.91x10 mm |
HiramekiWorksで軽量化したモデル 最大変位:3.31x10 mm |
Fig.10およびFig.11より、HiramekiWorksを使って軽量化したモデルは、自分で軽量化したモデルと同程度の体積ですが、最大変位量は小さくなっています。最大変位量については、原型モデルよりも小さいです。このことから、HiramekiWorksを使ったモデルは、剛性を上げてかつ軽量化することができたと言えます。
このようにHiramekiWorksでロボットアームの軽量化に取り組んでみて、素人の自分でも約1週間でソフトウェアの使い方を覚え、簡単ではありますが軽量化モデルを作成できました。もちろん実際に現実的な形状を作るにはより多くの試行錯誤が必要になりますが、HiramekiWorksは試行錯誤のヒント、すなわち“閃”を与えてくれると思います。
[From N. Hiramoto]
第1・第3木曜日配信!
SBDメールマガジンより、
最新の技術コラムをお届けします。
Analysis Case
解析事例
Analysis Case
解析事例
解析事例


Topics
トピックス
イベント・セミナー
シミュレーションに関するイベント・セミナー情報をお届けいたします。
2025年06月25日
2025年06月25日
2025年06月25日
トレーニング
SBD製品各種の操作トレーニングを開催しております。
2022年11月02日
2022年03月04日
2022年03月04日
技術コラム
シミュレーションに関する基礎知識や、製品の技術的なノウハウが満載の技術コラムをお届けいたします。
2025年07月08日
2025年07月08日
2025年07月04日
Topics
トピックス
トピックス


イベント・セミナー
シミュレーションに関するイベント・セミナー情報をお届けいたします。
2025年06月25日
2025年06月25日
2025年06月25日
トレーニング
SBD製品各種の操作トレーニングを開催しております。
2022年11月02日
2022年03月04日
2022年03月04日
技術コラム
シミュレーションに関する基礎知識や、製品の技術的なノウハウが満載の技術コラムをお届けいたします。
2025年07月08日
2025年07月08日
2025年07月04日